5 min read
Building a safer workplace: a step-by-step guide for effective safety risk management
By: Lucidity Team on Apr 2, 2025 2:42:47 PM
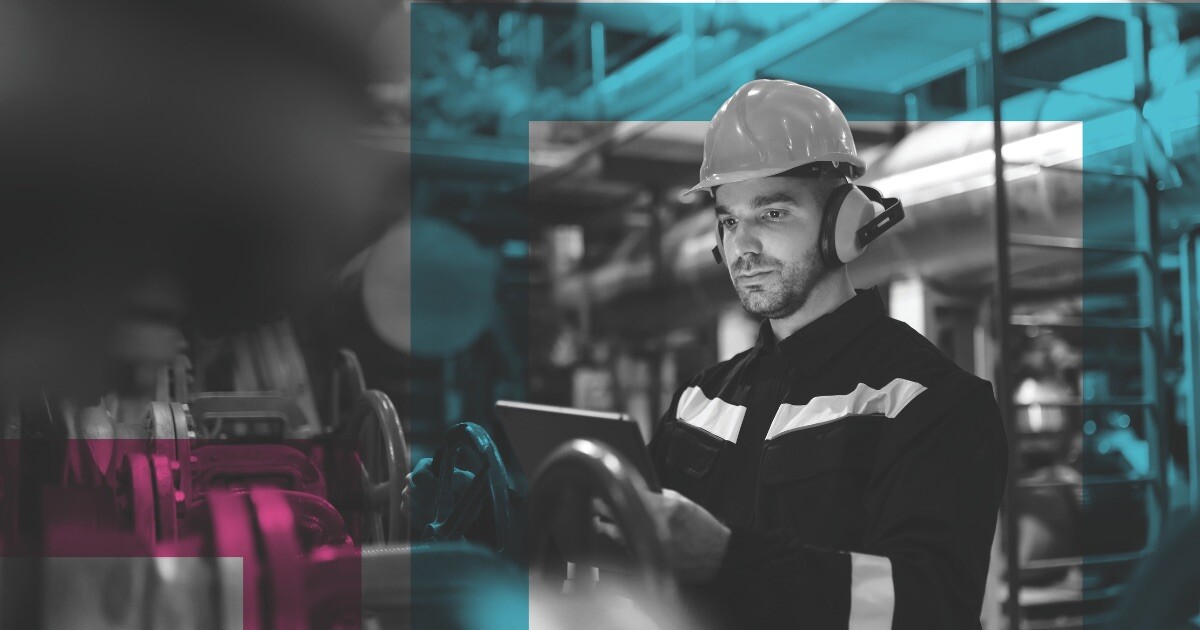
Workplace incidents can significantly impact an organisation's employees, operations and reputation. When the same types of incidents recur, the risks multiply, increasing potential harm and financial costs. A proactive approach to safety, focused on identifying root causes, implementing corrective actions and fostering a strong communication plan, is essential to prevent repeat incidents.
Here’s a practical guide for Australian organisations to create a robust safety risk plan.
1. Identify the root cause
The first step in preventing recurring incidents is to understand why they happen. Conduct a thorough investigation into each incident to reveal underlying causes, which may include inadequate training, outdated equipment or unclear safety protocols. Investigating may also uncover larger systemic issues, such as excessive employee fatigue caused by scheduling or workload, that contribute to the problem.
Collecting and analysing data is critical in this process. Gather incident reports, conduct interviews and review work processes to spot patterns and contributing factors. Common root cause analysis techniques, like the five whys, help dig deeper into an incident's underlying causes rather than merely addressing symptoms. For instance, asking "why" five times about a machinery breakdown could reveal an overlooked maintenance need or a training gap in equipment handling.
Practical tip: keep data analysis central to the root cause process. Use tools like Pareto charts, fishbone diagrams or failure mode and effects analysis (FMEA) to visualise and assess patterns in incident data.
2. Develop a corrective action plan
Once you’ve identified the root cause, it’s time to develop a corrective action plan tailored to address the specific risks. Prioritise corrective actions based on their impact on safety and likelihood of success. The plan should aim to eliminate hazards or, at minimum, reduce risks to acceptable levels.
Consider using the hierarchy of controls, which offers a proven approach to minimising hazards, ranked from most effective to least effective:
- Elimination: removing the hazard entirely
- Substitution: replacing hazardous materials or processes with safer alternatives
- Engineering controls: isolating people from the hazard through structural changes
- Administrative controls: updating processes or policies to reduce risk exposure
- Personal protective equipment (PPE): providing equipment to protect employees, though this should be a last resort as it does not eliminate the hazard
3. Implement the corrective action
After developing the plan, ensure it is properly implemented. Assign tasks with clear deadlines and provide employees with the resources and support they need to carry out corrective actions effectively. Using environmental, health and safety (EHS) software can streamline the tracking process, keeping everyone informed of deadlines and completion statuses in real time.
Once corrective actions are in place, track their effectiveness by measuring metrics such as incident frequency, completion of safety training or adherence to new policies. This measurement step ensures your corrective actions work in practice, not just in theory.
Practical tip: use a centralised tracking system or software to monitor the progress of each corrective action. Set automatic reminders to ensure timely follow-ups on open items and keep your team accountable.
4. Communicate changes and lessons learned
Clear communication is vital to a successful safety risk plan. Share updates and lessons learned with employees at all levels to keep everyone informed about changes to safety policies and procedures. Ensure managers and supervisors fully understand these changes so they can communicate them effectively to their teams.
Use a variety of communication tools such as visual aids, safety videos and real-life examples of incidents to make safety messaging relatable and engaging for employees. Ongoing updates reinforce the importance of safety and highlight the organisation’s commitment to protecting employees.
Practical tip: consider holding regular safety meetings or toolbox talks that provide updates on safety improvements, highlight resolved hazards and offer reminders of best practices.
5. Review and adjust as needed
Safety risk planning is an ongoing process. Regularly review the corrective actions implemented and adjust as necessary based on new insights or changing circumstances. Periodic audits can reveal any new hazards that may have arisen and help refine your safety policies to keep pace with business changes.
Practical tip: set a schedule for reviewing and adjusting your safety risk plan, ideally on a quarterly or annual basis, to ensure it remains effective and aligned with evolving workplace needs.
Build a safer workplace with Ideagen Lucidity
Ideagen Lucidity can help your organisation manage workplace risks more effectively. To find out more, simply contact our dedicated team on 1800 595 241 or support.lucidity@ideagen.com.
Disclaimer: This article is intended to provide general information on the subject matter. This is not intended as legal or expert advice for your specific situation. You should seek professional advice before acting or relying on the content of this information.
Related Posts
Four tips for implementing effective corrective actions
In high risk workplaces like construction sites, mines and factories, safety isn't just a priority,...
Beyond Identification: Empowering Safety Through Critical Control Management
Understanding the activities within your business that pose the greatest risk to your personnel...
A guide to health and safety inspections in the workplace
A workplace health and safety program consists of many processes and procedures, all of them...