6 min read
Four tips for implementing effective corrective actions
By: Lucidity Team on Jan 31, 2025 2:39:07 PM
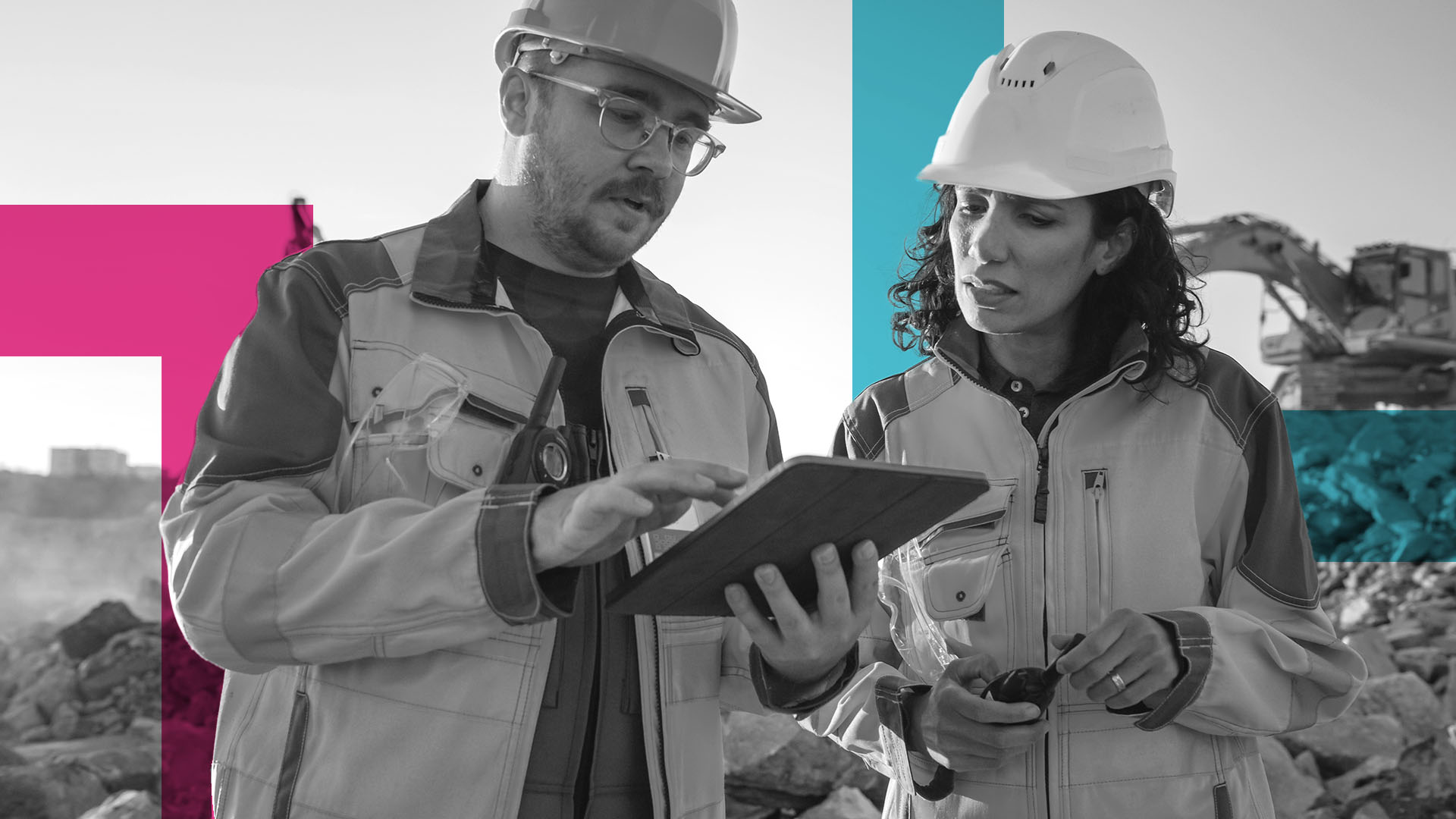
In high risk workplaces like construction sites, mines and factories, safety isn't just a priority, it's a lifeline. Crafting a robust corrective plan of action for safety risks is essential to prevent incidents from occurring, safeguard workers and ensure smooth operations.
Workplace incidents: the impact and the need for action
Workplace incidents can significantly impact an organisation's employees, operations and reputation. The risk is especially high when the same types of incidents occur repeatedly. When an incident happens, it is crucial to identify the root cause, develop a corrective plan of action and implement changes to prevent similar incidents in the future. Below are four practical steps for implementing corrective actions that prevent workplace incidents from recurring.
Tip one: identify the root cause
Understanding the underlying reasons for an incident is essential to prevent it from happening again. A thorough investigation into the incident can help identify contributing factors such as inadequate training, faulty equipment or ineffective policies or procedures.
An investigation can also uncover systemic issues that may have contributed to the incident. For example, if an incident occurs due to employee fatigue, it may indicate a more significant problem with workload or scheduling. Identifying these underlying issues is vital to prevent similar incidents from happening in the future.
Collecting and analysing data is an integral part of the root cause process and involves reviewing incident reports, conducting interviews with employees and analysing work processes. Analysing this data can help identify patterns and trends, providing insights into the underlying causes of the incident.
There are several popular root cause analysis methods, including the Pareto chart, 5 Whys, fishbone diagram, scatter plot diagram, and Failure Mode and Effects Analysis (FMEA). Among these, the 5 Whys technique is a widely used, simple and effective method for identifying the underlying causes of a problem to determine the root cause.
Tip two: develop a corrective plan of action
After identifying the root cause, the next step is to develop a corrective plan of action. During the development process, it is essential to prioritise actions based on their potential impact on safety and the likelihood of success. It is also necessary to set realistic timelines for implementing the corrective actions.
To ensure similar incidents do not occur, the corrective plan of action must address the underlying issues that led to the incident and lay out specific measures to prevent their recurrence. One effective way to apply preventive measures is through the hierarchy of controls. The hierarchy is a system that minimises or eliminates workplace hazards and consists of five levels: elimination, substitution, engineering controls, administrative controls and personal protective equipment (PPE).
Among these levels, elimination and substitution are considered the most effective methods since they remove the hazard or replace it with a safer alternative. For instance, hazardous chemicals can be eliminated from a process or substituted with non-toxic materials. However, PPE is less effective because it only shields the individual wearing it and does not eliminate the hazard.
Tip three: implement the corrective actions
To prevent workplace incidents from recurring, it is essential to implement the right corrective actions. Involving employees in the process and providing them with the necessary resources and support is crucial to ensuring success. This not only gives employees confidence in the solution but also ensures it works in practice.
First, set up a method of assigning corrective actions and notifying the task owner and the person’s supervisor of upcoming deadlines. On-time resolution of corrective actions is tightly correlated with a measurable reduction in workplace incidents, yet it can be difficult to achieve with all the other demands on operations and EHS teams. A best practice is to assign, notify and track corrective actions with EHS software that gives the relevant people visibility at all times.
Once the action is completed, measure its impact. This step may involve tracking metrics such as the number of incidents or near-misses, the completion of training programs or the implementation of new policies and procedures. This is also easily accomplished with EHS software.
When implementing a corrective plan of action, it is vital to consider any unintended consequences. For example, if a corrective action involves adding a new safety procedure, how might that impact productivity? It's always important to find a balance and ensure the corrective actions are practical and feasible.
Tip four: communicate changes and lessons learned
Communication plays a vital role in the prevention of workplace incident reoccurrence. Effective communication entails sharing updates and lessons learned with all employees in the organisation, regardless of their position, to ensure everyone is aware of new policies and procedures.
Before speaking with employees, ensure all managers know and understand the changes. These frontline leaders can help guarantee the consistent implementation of the changes throughout the organisation.
Communication should be continuous and include frequent updates on progress and any changes to policies or procedures. Visual aids, safety videos and delving into past incidents can improve the effectiveness of this communication and make the message resonate with employees.
Conclusion
Preventing workplace incidents from reoccurring requires a proactive and systematic approach. By identifying root causes, developing and implementing corrective actions, and maintaining open communication, organisations can create a safer, more compliant workplace. Remember, safety is not a one-time effort but a continuous commitment to improvement.
Want to learn more about how EHS management software can help you implement effective controls to reduce safety risks?
The team at Ideagen Lucidity is here to help. Contact us today on 1800 595 241 or contact.lucidity@ideagen.com.
Disclaimer: This article is intended to provide general information on the subject matter. This is not intended as legal or expert advice for your specific situation. You should seek professional advice before acting or relying on the content of this information.
Related Posts
Building a safer workplace: a step-by-step guide for effective safety risk management
Workplace incidents can significantly impact an organisation's employees, operations and...
Beyond Identification: Empowering Safety Through Critical Control Management
Understanding the activities within your business that pose the greatest risk to your personnel...
Incident rate benchmarking: a guide for Australian organisations
Workplace injuries and illnesses significantly impact an organisation’s overall health. Incidents...